- Joined
- Jan 9, 2019
- Messages
- 825
- Reaction score
- 4,137
Thanks BC.
Another FF. I think I've got it now.
Another FF. I think I've got it now.
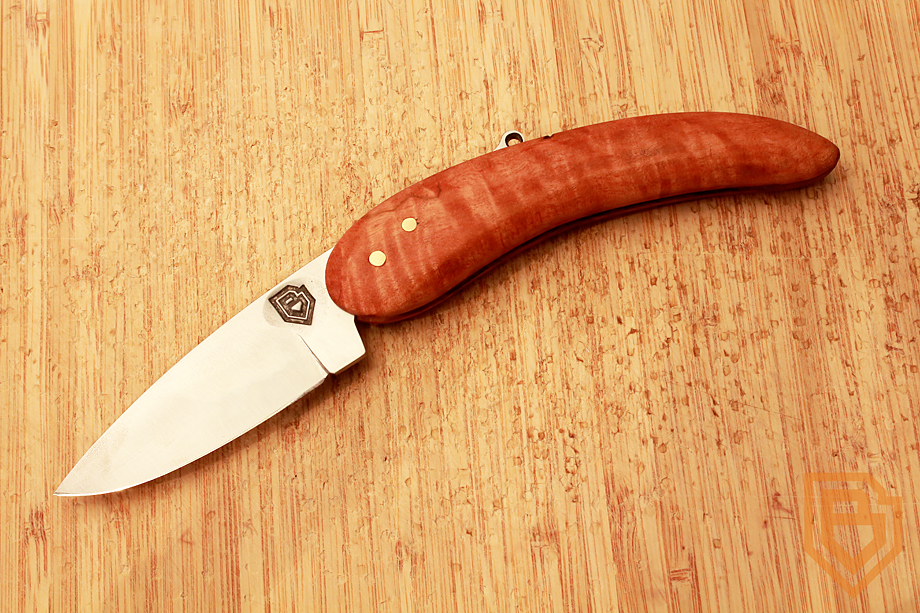
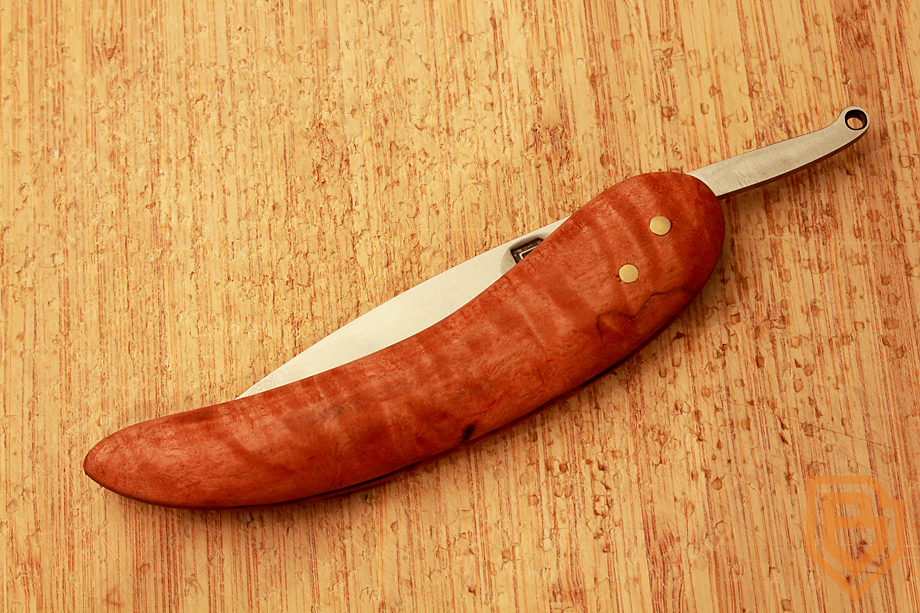
Patrick1 said:Would any of you fine knife makers be willing to make me a Navy Mark III knife? If so, give me a price. By PM is fine. I'd like to own some of the craftsmanship I've seen on here.
That's the one. That's the blade type I'd like. The grip...it's gotta be wood. Seen so many beautiful ones on here.7.62marksman said:
Sandbagger said:While showing a quick video of how my latest knife works, I thought I'd have a quick play around with a free video editor and chuck in the intro clip. I need to learn all the tricks of a full version video editor, but that's a way off yet.
Whaddya reckon?
Baz.
[video=480,360]https://youtu.be/qTcEreEX5gA[/video]
shakergt said:Look what you guys have gone and done. Got me knife making now. I have wanted to give it a go for ages. This is my second attempts the first one I stuffed up. Anyway this started life as an old edger blade. It has been heated and quenched twice. I want to get the edge a bit better before the final heat and oil quench. As I don't have a polisher what do you guys recomend for the finish off. Any advice will be greatly appreciated.
https://www.prospectingaustralia.com/forum/img/member-images/10374/1563182412_20190715_165623.jpg
https://www.prospectingaustralia.com/forum/img/member-images/10374/1563182413_20190715_165614.jpg
https://www.prospectingaustralia.com/forum/img/member-images/10374/1563182414_20190715_165618.jpg
Sandbagger said:shakergt said:Look what you guys have gone and done. Got me knife making now. I have wanted to give it a go for ages. This is my second attempts the first one I stuffed up. Anyway this started life as an old edger blade. It has been heated and quenched twice. I want to get the edge a bit better before the final heat and oil quench. As I don't have a polisher what do you guys recomend for the finish off. Any advice will be greatly appreciated.
https://www.prospectingaustralia.com/forum/img/member-images/10374/1563182412_20190715_165623.jpg
https://www.prospectingaustralia.com/forum/img/member-images/10374/1563182413_20190715_165614.jpg
https://www.prospectingaustralia.com/forum/img/member-images/10374/1563182414_20190715_165618.jpg
Here's a few tips for you mate.
Edger blade - unknown qualities, plus it is likely to have hit rock and concrete very hard multiple times, so is likely to have fractures in it.
Heat treating - you need to leave the cutting edge about 1mm thick to survive the heat treating process without buckling, bending and cracking.
The 1mm edge should have the grind lines going length ways down the blade, while the sides of the knife should have them going across the knife. This stops stress risers and a potential crack from forming and continuing all the way over.
1075 is a high carbon steel, which is readily available through Gameco Artisan Supplies. It is cheap and the industry standard. 40 bucks should get you a bar of about a metre to make some reasonable knives out of.
You can also get Rynowet sandpaper from Gameco, which lasts three times longer than that Bunnings crap.
Getting your steel too hot in the heat treat before quenching in warm canola oil, can be just as bad as not getting it hot enough. You only need to bring it up to the non-magnetic, critical temperature and no further. For 1075, that is 815 degrees. Watch you don't get the tip and the edge too hot. Put it in and out of the heat, watching the thin material, and let the thicker parts of the blade creep up to temperature slowly. When you quench, get it straight out of the heat and straight in the oil. Milliseconds count. Gently wave the knife in the oil, like you are slicing it, to break up the steam-jacket that may slow the rate of cooling. Side to side is a big no-no, as you may cool one side of the blade faster than the other and get a bend.
Stick it in the oven for two hours at 210 degrees Celcius for tempering. Any clean parts of the blade should come out a golden, straw yellow. If it turned blue, you've got too hot and you need to go all the way back to heat-treating again.
After heat treat, then you can do the post-heat treat grind to refine your geometries and bring the bevel and edge down to zero, ready for sharpening. All the while you are doing this finishing grind you must constantly dunk it in water every grind, so you don't cook the blade. If you turn any part of the blade blue, you need to go back to heat treat, but if the edge is now zero, you need to grind it off to 1mm again or it will split warp and buckle in the HT.
If you finish your grind to 100 grit or better, then you can clamp your blade to a block of wood, wrap some rynowet at 120 grit around a piece of aluminium bar stock and sand length-ways to get the scratches out. It's hard work and every knifemaker hates it, but it's the last 5% that makes 80% of the difference. Progress up through the grits, finishing on at least 320 grit, but you can go higher for a mirror finish if you want.
I hope this helps.
Baz.
shakergt said:Thank you the info Baz. I have gone with steel and info from Gameco. My blade went peacock purple. Is that bad? This knife will be used as a skinner.
Enter your email address to join: