hyperscott
Scott
Hi Guys,
Planning to take my first trip out with My Dad and Family for an attempt at Fossicking, Tomorrow.
So been going madly through all my Kit to see what I had that I could take, (including perusing the forum and YouTube to see what i should consider.)
Then playing with my 3D printer last night I thought id see what I could make that might be useful from stuff I had around my work shop.
An old Hard Drive / Disk later and I have black sand magnet.
1) Hard drive magnets from old hard drive/hard disk
2) Piece of string that is strong enough to lift the magnet from its payload
3) Non magnetized separating rings from between hard drive plates
I designed up in 3D Builder(3D design software built into windows 10) a magnet holder for hard drive magnets, and a canister or cylinder to house them.
Model is available @ Thingverse - thing:2011502 ( Will add URL once I have completed my 10 posts )
Please feel free to suggest modifications or take it and edit the files.
Regards
Scott
( HyperScott / Blazesurfer )
Planning to take my first trip out with My Dad and Family for an attempt at Fossicking, Tomorrow.
So been going madly through all my Kit to see what I had that I could take, (including perusing the forum and YouTube to see what i should consider.)
Then playing with my 3D printer last night I thought id see what I could make that might be useful from stuff I had around my work shop.
An old Hard Drive / Disk later and I have black sand magnet.
1) Hard drive magnets from old hard drive/hard disk
2) Piece of string that is strong enough to lift the magnet from its payload
3) Non magnetized separating rings from between hard drive plates
I designed up in 3D Builder(3D design software built into windows 10) a magnet holder for hard drive magnets, and a canister or cylinder to house them.
Model is available @ Thingverse - thing:2011502 ( Will add URL once I have completed my 10 posts )
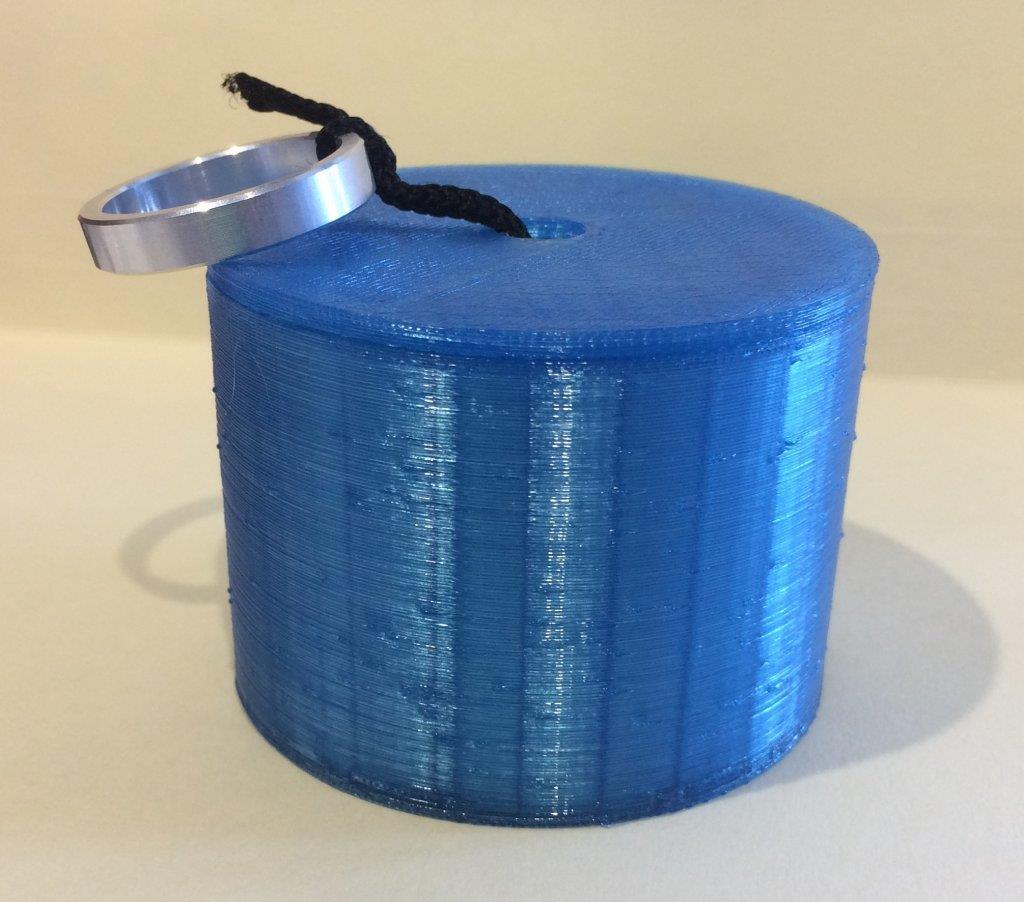
Please feel free to suggest modifications or take it and edit the files.
Regards
Scott
( HyperScott / Blazesurfer )